Safer products through better design
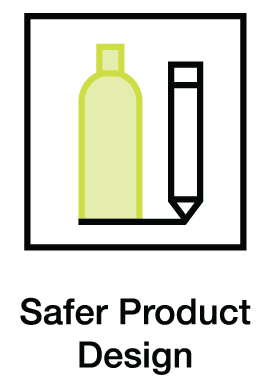
The fourth pillar of leadership: safer product design
Turn company commitments to sell products with safer ingredients into results on store shelves. This is one of the most challenging Pillars of Leadership because it deals directly with how companies make decisions about product composition. However, it can also be the most exciting pillar because it presents opportunities for businesses to innovate and gain a competitive edge.
Safer Product Design involves:
- understanding your chemical footprint.
- leveraging this understanding to set specific improvement targets for new and existing products.
- establishing a methodology for eliminating toxic chemicals and selecting safer alternatives.
- providing relevant staff with the resources and direction they need.
- tracking progress against your goals.
There are a number of factors to consider when implementing the Safer Product Design pillar. EDF has advice on how to get started.
Understanding your chemical footprint and setting specific goals for improvement:
-
What chemicals are of concern?
Chemicals of concern are those that are linked to major acute and chronic health and environmental impacts such as allergenicity, reproductive toxicity, cancer, and endocrine disruption. The good thing is that you don’t have to do the work all by yourself to identify such chemicals; a number of authoritative scientific and regulatory bodies around the globe continuously review the potential hazards of chemicals in commerce. The scientific literature is also helpful.
-
What is your current chemical footprint?
Once you’ve prioritized health and environmental impacts, you can calculate your chemical footprint, or the amount of toxic chemicals used in your products and their production processes. When you are focused on Safer Product Design, you are focused on reducing your chemical footprint. So, it is important to know what your baseline chemical footprint is – how many toxic chemicals you are dealing with in your product portfolio, where they appear, and at what volume. Robust supply chain transparencyis very helpful here.
-
What are your improvement benchmarks?
For example, a company may set a goal of selling products free of PBTs (persistent, bioaccumulative, and toxic chemicals). Then it may set an objective to phase out of a set of PBTs by a certain date or to reduce the overall volume of PBTs by a certain date. Defining your goal in specific terms helps you better understand the tools and expertise you will need.
-
Where should you act first?
Will you focus only on new products or on reformulating existing products or both? Will you tackle your global portfolio or begin in one jurisdiction? Ambitious goals to eliminate all toxic chemicals in your business are admirable (and welcomed), but it’s difficult to tackle everything at once. To start, you could focus on eliminating toxic chemicals that appear most frequently in your products or that appear in the highest volumes. Or you could start by tackling product categories that make the biggest contribution to your chemical footprint. Contextual factors, such as which product types or components directly expose consumers and/or manufacturing workers, can also help you prioritize action. Finally, external factors, such as products or chemicals receiving the most regulatory and NGO pressure, are also helpful. Wherever you decide to begin, it is critical to map out a plan, with deadlines, to create accountability and to determine what resources you will need.
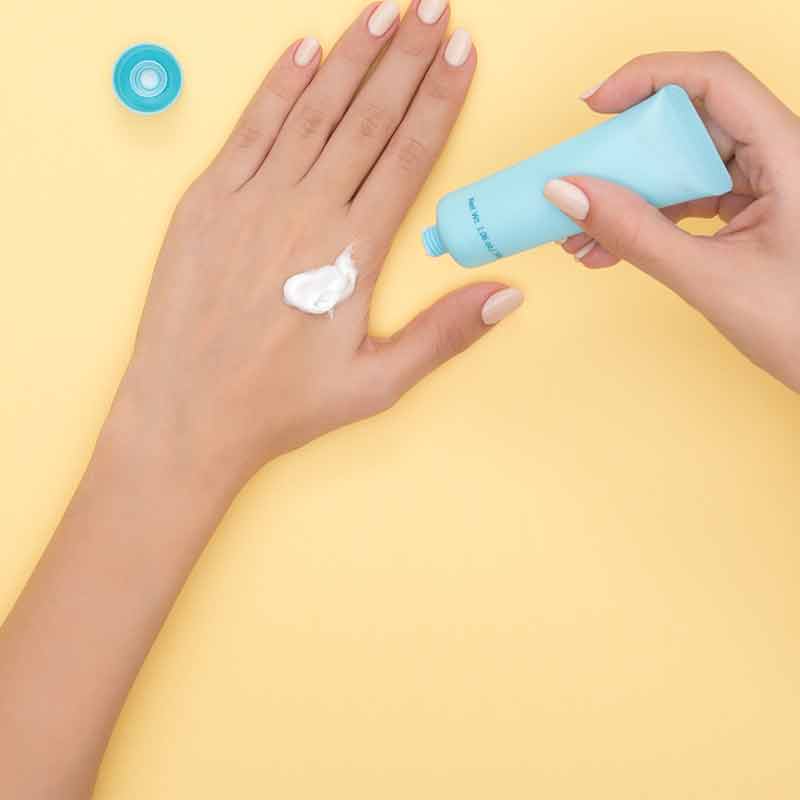
Turning goals into action:
-
What is your approach to evaluating chemicals?
Is your aim to move to ingredients that don’t appear on authoritative hazard lists or to select ingredients based on complete safety profiles that are backed by robust data or ideally do both? Will you rely on outside expertise, e.g. working with a consultant or a certification program like Cradle to Cradle? Or will you build in-house capabilities and processes?
-
What changes need to be implemented in your product development process to meet your new goals?
Do functional specifications for product components and materials need to be updated? Do new activities need to be considered during your product development stage-gate process? Achieving your safer ingredient goals may require revising the responsibilities of relevant business units and possibly bringing additional expertise on-board.
-
Do you have the tools and infrastructure needed?
There are big differences between ingredient sourcing changes, product redesigns or reformulations, and creation of entirely new product lines. Success requires considering how to accomplish such different scenarios.
-
What roles and responsibilities are required?
There are many internal business functions that should be involved in achieving your safer product objectives including research and development, marketing, procurement, and sustainability. The specific responsibilities of each business function will need to be identified and adopted. For example, the sustainability team may be responsible for setting objectives and evaluating progress, while the procurement team may be responsible for communicating new expectations to suppliers. Similarly, a company should identify outside entities that can support implementation, such as tier one suppliers, professional societies and trade associations, chemical assessors, and public interest groups.
-
What performance metrics should you track?
Performance metrics are critical for re-evaluating the ambition of your goals and the effectiveness of your implementation strategy. For example, you might want to track changes in the number of suppliers using a particular toxic chemical over time or the rate at which products are being redesigned. Returning to your chemical footprint and tracking its decline is a critical component of tracking progress.
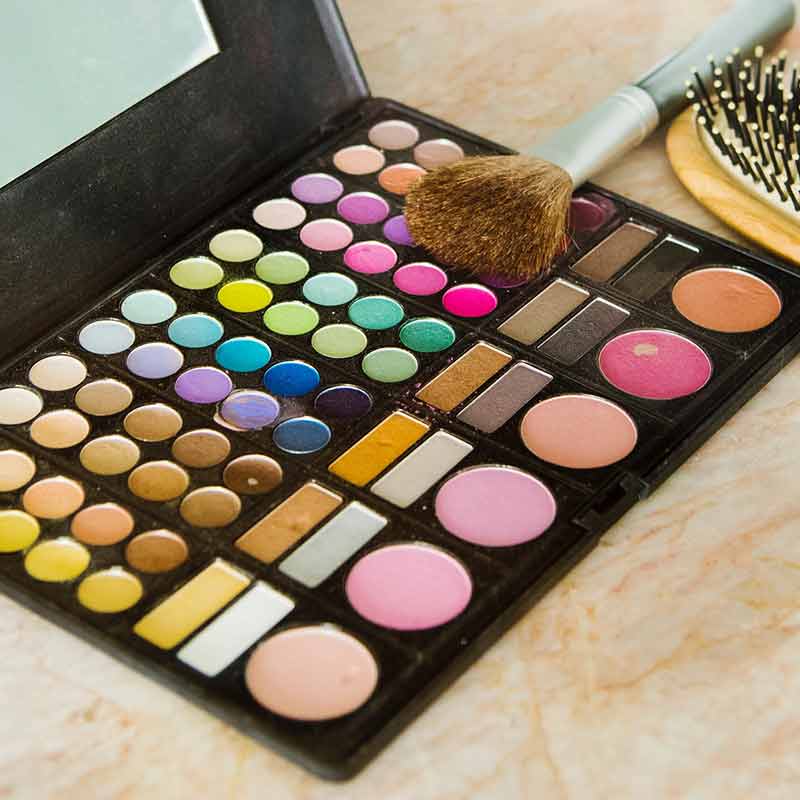
Overcoming hurdles on the path to leadership
-
Make a plan
Planning up front can help you anticipate and prepare for potential issues before they arise. Set specific, measurable objectives. Identify early on the key internal stakeholders who need to be involved and their responsibilities. Perform a gap analysis on the resources and competencies your company has today. Build an understanding of the tools and external resources available to you.
-
Be patient and persistent
Finally, never lose sight of your ultimate goal of creating a safer marketplace. Change doesn’t happen overnight, so returning to your goal and mission often will fortify morale when you’re in the middle miles.
It may feel daunting to revamp the way your company selects ingredients, but the pay-off is worth it. You can avoid costly reformulations every time a new chemical regulation is announced, and you can build customer loyalty.
Resources
The OECD Substitution and Alternatives Assessment Toolbox: A Tool for Safer Chemicals in Products
Report: Smart Innovation: The Opportunity for Safer Preservatives
Go to: The fifth pillar of leadership: public commitment